Fastener Failure: What You Need to Know
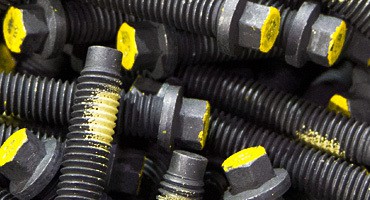
There are three common attributes that all threaded fasteners share.
1. All threaded fasteners loosen.
Threaded fasteners are designed to be reversible. Often this is a desirable quality –particularly when service removability is a necessity – but fasteners can and do come loose on their own, which can cause serious, expensive, and sometimes dangerous problems. Loose fasteners on an assembly can lead to vibration, noise, and overall quality issues, and ultimately lead to fastener failure.
2. All threaded fasteners have the potential for locking failure.
Fasteners can fail due to vibration, shock, or any number of environmental factors that an assembled product is exposed to. Products with mechanical or moving elements, or those that come into contact with moisture or work under air and fluid pressures, are particularly susceptible. While we put our faith in fasteners as a highly integral part of any assembly, there are a few things that should be noted about fasteners and fastener failure:
- When friction drops in the threads of a seated fastener, or under the head, that fastener will start to loosen even if the bolt was properly tightened.
- Once side-sliding starts it takes less than 100 cycles of vibration to loosen a fastener.
- And it takes less torque to loosen a fastener than to tighten it.
As shown in this Laboratory Demonstration, ND Expand-A-Seal expands volumetrically 20-50%
3. All fastening points are potential leak paths.
Fastening points are the weak spots in any assembly. Leaks, particularly in assemblies that involve or must endure air or fluid pressures, can develop at fastening points using the helix of the threaded fastener like a canal. In the case of hydraulic assemblies, and other assemblies that require and utilize pressure, this can create a serious problem in the performance of the product over time.
Because of these common attributes of threaded fasteners, new and better developments in fastening technology are essential to the progress of modern industry. For over 50 years thread adhesives have been used to effectively fortify fastener reliability. Adhesives have been used to protect joints and guarantee that fastening components will not come apart even if a joint or fastener has been inadvertently loosened. Even when joints squeak and rattle, a clear indication of fastener failure, adhesives help keep joints and fasteners from separating and causing much more severe failures.
The use of fastener adhesives and coatings during assembly has become increasingly important to ensure the integrity and reliability of those assemblies, while also helping to reduce variation in clamploading and improve corrosion resistance and torque tension relationships. Furthermore, assemblers have found that the pre-application system ofutilizing fastener adhesives saves time and money on the assembly line, as pre-applied adhesives are typically less expensive than bottled adhesives and pre-application eliminates the unavoidable errors in the time-consuming process of on-line adhesive application. Pre-applied locking and sealing coatings are used regularly in many industries, including: automotive, electronics, aerospace, marine, construction, and appliance, to name just a few.
As pre-applied fastener adhesives have become more necessary in the efforts of manufacturers to meet modern assembly requirements, the micro-encapsulation of adhesive components in pre-application technology has become the method of choice as a fast, clean and effective way of utilizing chemical bonding during assembly. The premise of micro-encapsulation is that a 2 part adhesive, typically epoxy, acrylic or similar, is applied to the fastener in a pre-application process. But, unlike the result of bottled adhesive applications, the 2 components of the adhesive do not mix during the application of the adhesive to the fastener. Instead, the components are dry-fused to the fastener and kept separated by micro-encapsulation. That is, simply stated, one component is contained within tiny spheres, micro-caps or micro-spheres, and kept separated from the second activating component until assembly occurs. The dry-fusing of the components to the fastener ensures that the coated fastener remains dry to the touch and clean to handle, and that the micro-encapsulation technology will not activate even if handled roughly. When assembly does occur, the force of the fastener engagement breaks open the micro-caps and allows the adhesive to activate, creating a positive bond.
Most pre-applied, micro-encapsulated fastener coatings are designed to serve a single purpose, which is to lock a fastener in place, extremely well. With this understanding it is easy to see how many pre-applied micro-encapsulated adhesives, one of the most effective locking technologies available, may not provide the most effective air and fluid seal.
While all thread adhesives help to give some protection against leakage at fastening points by providing a kind of dam of adhesive material inside the fastener threads, adhesives intended only for locking and bonding are not designed to form a gasket that ensures sealing under air and fluid pressures. Even the most formidable bonds created by threadlockers leave miniscule spaces within the threads of a seated fastener, allowing for gas and fluid leakage. Gas and fluid leakage can become a particularly difficult problem at fastening points when subjected to pressure strained conditions, such as in compression tanks or air brakes. Often other methods of sealing are employed, mastics, form-in-place gaskets or other materials designed specifically to provide leakage protection, where a highly reliable seal is necessary.
But now, thanks to advancements in micro-encapsulation technology, a new 2 in 1 locking and sealing micro-encapsulated formula is available to assemblers, ND Expand-A-Seal ES0105®. This pre-applied, high-powered, microencapsulated thread-locking solution also provides an effective air and water tight seal even under the strain of gas and fluid pressure.
A product of ND Industries®, a global leader in fastening adhesive production and research, ND Expand-A-Seal ES0105 can be applied to interior or exterior threaded fasteners of all sizes. And, because it contains all of the components of the adhesive needed for activation, ND Expand-A-Seal only needs to be applied to either one of any two mating, threaded parts for effective sealing and locking.
With the implementation of ND Expand-A-Seal, concern about leakage and the use of multiple methods of locking and sealing on a single application becomes a thing of the past. When ND Expand-A-Seal’s chemical adhesive agent is activated it simultaneously expands volumetrically 20-50%, filling any gaps and voids within the fastener threads and creating a positive seal against air and most automotive fluids. ND Expand-A-Seal will even effectively fill gaps resulting from the use of oversized fastener threads or fastener deformation that occurs during welding. The seal created by this breakthrough technology will endure even under the force of air and fluid pressures, and has been successfully tested on straight threads under the strain of 115psi without compromise to its sealing capacity.
As with other micro-encapsulated coatings, ND Expand-A-Seal has low prevailing on torque, so assembles easily with common hand tools. However, the chemical reaction that takes place upon mechanical fastening is so rapid, and its strength so considerable even before fully cured, that exceptional breakaway torque values are achieved within as short a time as one hour after activation.
No heat curing is required for fasteners coated with ND Expand-A-Seal; full cure is achieved in 24 hours at room temperature.
As a locking agent, fully cured ND Expand-A-Seal creates a bond comparable in strength to most epoxy threadlockers.
The cross-linked molecular structure of ND Expand-A-Seal makes it one of the most resistant types of fastener adhesive available. Fully cured, ND Expand-A-Seal’s sealing and locking power is unaffected by exposure to foreign substances, including: oil, gasoline, salt-spray, acids, solvents, water and more.
ND Expand-A-Seal can be used to seal and lock almost any critical application where shock, vibration and fluid or air pressure could cause a fastener to loosen or a joint to leak and is ideal for applications where fittings must stay securely locked while under constant stress. Typical applications of this technology include: drain cocks, engine pipe plugs, air filtering connectors, compressor fittings, cooling connectors and much more.